A few things to mention about materials (especially PLA)
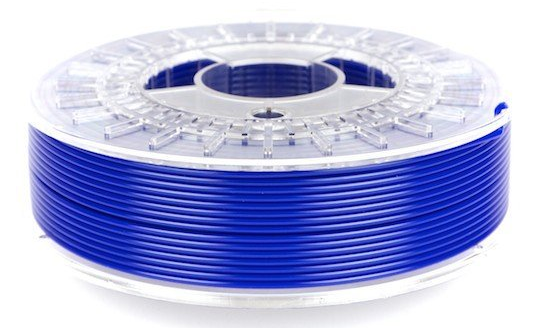
We use 3D printers to produce our products. There are different types of printers and countless different processes. We have specialized in what is sometimes revered to as FFF (fuse filament fabrication). The process is rather cost effective and uses a simple process of depositing a thermoplastic material layer by layer.
3D printing technology used to be locked down by patents for decades, limiting the technology to large and costly machines. Once those patents ran out, a new generation of desktop printers started to emerge. These machines are rather simple in design, but manage to output parts with astounding quality. Also, due to the small investment costs, the process can now be parallelized which has a profund influence on production costs.
At the core of all this, is the material. After all, it is the material in combination with a specific design that enables a desired functionality. And today, in 2020, PLA or 'polylactic acid' is one of the most widespread materials in desktop 3D printing.
PLA outperforms almost any other material in this category in terms of strength and stiffness (yes, those are two different things ;)). An interesting comparison is published by simplfy3d here. This is especially true if we take into account the directional dependency of the material properties which is introduced by the FFF process. Out of plane strength, i.e. layer adhesion, suffers greatly for most materials. The overall knock down for PLA is relatively low.
PLA does however suffer from a significant drawback; low maximum service temperature. PLA softens at rather low temperatures (40°C-50°C). Parts printed in PLA should hence not be exposed to excessive heat from e.g. sun light.
What does that mean for the design? If certain components in a deisgn generate more heat than PLA can handle (from e.g. electric motors), other materials such as ABS should be considered. One such example are motor cages for nerf blasters. We print those entirely in ABS to ensure no heat is transferred to the PLA .
Neuer TextSources:
Top image: colorfabb.com
Filament Properties Table: https://www.simplify3d.com/support/materials-guide/properties-table/
Strength comparison video: CNC kitchen; https://www.youtube.com/channel/UCiczXOhGpvoQGhOL16EZiTg
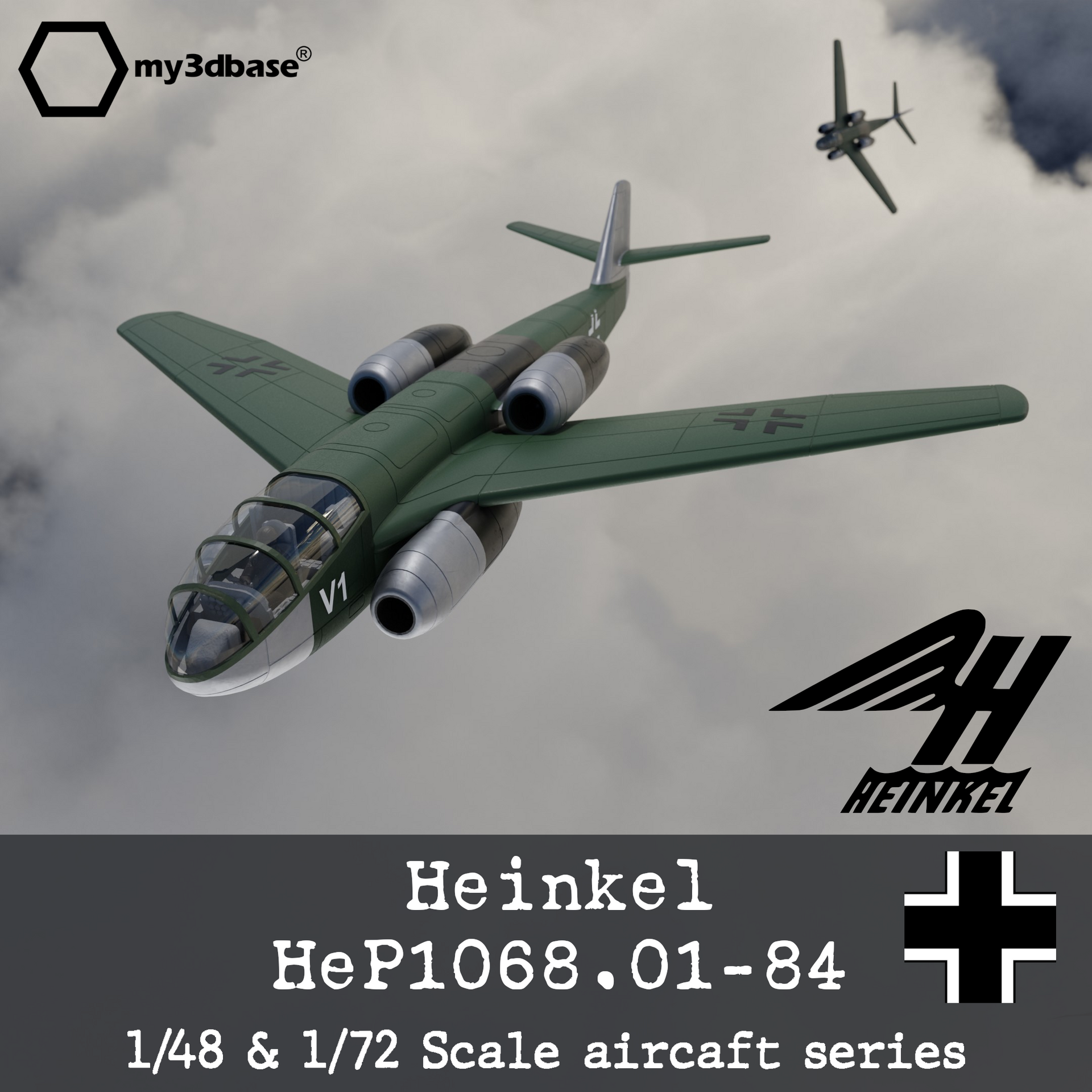
Bringing the Heinkel P.1068 to Life For aviation history enthusiasts and model builders, the Heinkel P.1068 is one of the lesser-known yet highly intriguing Luft ’46 aircraft concepts. Originally developed as a twin-engine competitor to the Arado Ar 234 , it evolved into a more advanced bomber featuring up to six engines. Though the He 343 project was ultimately canceled, the P.1068 survived in a different form—as a test aircraft built in collaboration with DFS (Deutsche Forschungsanstalt für Segelflug) . Now, you can bring this advanced jet bomber concept to life with our latest Heinkel P.1068-01 model kit , available exclusively at My3DBase .
Damit Eure Kekse mit unseren Backförmchen so richtig gut funktionieren haben wir für euch ein paar Tips zusammengestellt. Vorab einmal das Rezept: 100 g Butter 50 g Puderzucker (kann dem eigenen Geschmack angepasst werden) 30 g Ei 200 g Mehl Die Mengen können unter Einhaltung des Mischungsverhältnisses erhöht werden. Zunächst wird der Puderzucker mit der Butter vermengt. Danach wir das Ei hinzugegeben. Anschließend wird das Mehl untergehoben. Wichtig: Damit der Teig die richtige Konsistenz erhält sollte er gekühlt werden; ca 30min im Gefrierfach oder 1-2 Stunden im Kühlschrank.